Pass Six Sigma LSSBB Exam in First Attempt Guaranteed!
Get 100% Latest Exam Questions, Accurate & Verified Answers to Pass the Actual Exam!
30 Days Free Updates, Instant Download!
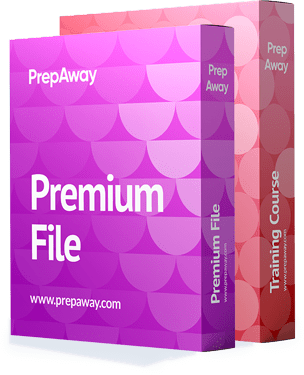
$19.99
LSSBB Premium Bundle
$64.99
$84.98
- Premium File 300 Questions & Answers. Last update: Aug 31, 2025
- Training Course 45 Video Lectures
$84.98
$64.99
Last Week Results!

10
Customers Passed Six Sigma LSSBB Exam
Average Score In Actual Exam At Testing Centre
Questions came word for word from this dump
Get Unlimited Access to All Premium Files
Details
Purchase LSSBB Exam Training Products Individually
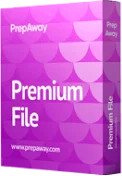
Premium File 300 Q&A
$65.99$59.99
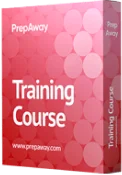
Training Course
45 Lectures
$27.49
$24.99
Why customers love us?
93%
Career Advancement Reports
92%
experienced career promotions, with an average salary increase of 53%
93%
mentioned that the mock exams were as beneficial as the real tests
97%
would recommend PrepAway to their colleagues